Papers by Prof Fatai O Aramide
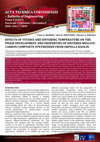
The effects of the addition of titania and sintering temperatures on the phases developed, physic... more The effects of the addition of titania and sintering temperatures on the phases developed, physical and mechanical properties of sintered ceramic composite produced from kaolin and spent graphite electrode was investigated. The kaolin and graphite of known mineralogical composition were thoroughly blended with 2 and 4 (vol.) % titania. From the homogeneous mixture of kaolin, graphite and titania, standard samples were prepared via uniaxial compaction. The test samples produced were subjected to firing (sintering) at 1300 ̊C, 1400 ̊C and 1500 ̊C. The sintered samples were characterized for the developed phases using x‐ray diffractometry analysis, microstructural morphology using ultra‐high resolution field emission scanning electron microscope (UHRFEGSEM) various physical and mechanical properties were determined. It was observed that microstructural morphology of the samples revealed the evolution of mullite, cristobalite and microcline. The mineralogical phase of the samples reveal...
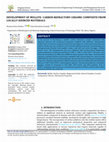
International Journal of Engineering Technologies and Management Research
In the pursuit of developing a mullite- carbon refractory ceramic composite with optimum physical... more In the pursuit of developing a mullite- carbon refractory ceramic composite with optimum physical and mechanical properties modified with additives, experimental studies were carried out using local materials from Nigeria's south-south and south-west regions. Kaolin clay was crushed to 2 mm and ball-milled into powder. Ground kaolin was homogeneously blended with graphite using a ball mill and sieved through a 300μm electric sieve. The homogeneous mix was combined with predetermined Magnesium Oxide proportions, compacted, and fired at 1300 °C, 1400 °C, and 1500 °C. Extensive tests followed, including X-ray diffraction (XRD) for phase analysis, ultra-high- resolution field emission scanning electron microscopy equipped with energy-dispersive spectroscopy (SEM-EDS) for microstructural morphology, and assessments of mechanical and physical properties. Findings indicated that additive inclusion spurred mullite phase development between 1300°C and 1500°C, enhancing their physico- mec...
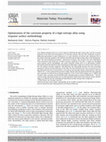
Materials Today: Proceedings, 2021
Laser Additive Manufacturing was used to fabricate AlTiCrFeCoNi high entropy alloy and the corros... more Laser Additive Manufacturing was used to fabricate AlTiCrFeCoNi high entropy alloy and the corrosion properties of the alloy were investigated in 3.5 wt% NaCl solution. The tests were conducted via potentiodynamic polarization at room temperature in a three-electrode cell system with a platinum wire as the counter electrode, Ag/AgCl as the reference electrode and the high entropy alloy as the working electrode. The electrochemical parameters; polarization resistance and corrosion rate were determined. These parameters help decide the corrosion resistance capability of the alloy. A model was developed using response surface methodology, and central composite design tools as an optimization method. The experimental and theoretical data using design of experiment's analysis of variance were used to predict the optimal corrosion properties and determine the relationship between the laser processing parameters and the corrosion behaviour of the alloy. The electrochemical tests were carried out on samples fabricated from the set of parameters; laser power and scanning velocity varied between 1400 and 1600 W at 8-12 mm/s derived from previous studies. Results from the model showed that the optimum laser parameter to yield the best corrosion properties in the 3.5 wt% NaCl medium was at 1500 W and 10 mm/s, with a corrosion rate of 0.003445 mm/yr and polarization resistance 0.00255 X.cm À2. The theoretical and the experimental data were in good agreement which shows that response surface methodology is an effective tool for modelling and optimizing the high entropy alloy's properties.
SSRN Electronic Journal, 2022
Materials Today: Proceedings, 2021

Journal of Alloys and Compounds, 2021
Abstract Corrosion is a conservational occurrence that has a large economic impact on most metals... more Abstract Corrosion is a conservational occurrence that has a large economic impact on most metals and its alloys because it destroys and deteriorates most materials by an electrochemical process through the reaction of these materials with the environment. High Entropy Alloys in aerospace applications react with the environment in applications such as jet engines, especially at elevated temperatures. Thus, the capacity of high entropy alloys to resist corrosion must be investigated to expand the application of this advanced material in the aerospace industry. In this comparative study, AlCoCrFeNiCu and AlCoCrFeNiTi High Entropy Alloy samples were fabricated by Laser Additive Manufacturing, particularly direct energy deposition and the corrosion behaviour of both alloys were examined and compared. The influence of the laser processing parameters on the microstructure and corrosion responses of the high entropy alloys in 3.5 wt% NaCl solution was also investigated. The microstructural morphologies were examined using an X-ray diffraction system (XRD) and Scanning electron microscope (SEM) equipped with Energy Dispersion Spectroscopy (EDS). The results showed that the Scan speed had the most influence on the microstructure and corrosion behaviour of the alloys. There was a strong relationship between the phase structure of the alloys and their susceptibility to localized corrosion. Therefore, it has been proposed in this study that the phase distribution within the alloys also influences the corrosion behaviour of laser deposited high entropy alloys.
Advances in High-Entropy Alloys - Materials Research, Exotic Properties and Applications, 2021
This study reviews the recent technological advancements in manufacturing technique; laser surfac... more This study reviews the recent technological advancements in manufacturing technique; laser surface modification and material; High Entropy Superalloys. High Entropy Superalloys are current potential alternatives to nickel superalloys for gas turbine applications and these superalloys are presented as the most promising material for gas turbine engine applications.
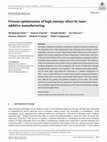
Authorea
Aerospace components and their coatings are required to possess excellent surface properties over... more Aerospace components and their coatings are required to possess excellent surface properties over a wide temperature range. Stainless steels, titanium, nickel superalloy, and more recently high entropy alloys (HEAs) have been used to improve the exterior properties of these components. In this study, AlTiCrFe-CoNi and AlCoCrFeNiCu HEAs were successfully fabricated using laser additive manufacturing to produce coatings on an A301 steel base plate. The influence of the laser parameters (laser power and scan speed) on the microstructure and hardness properties were also investigated. The results revealed that coatings homogeneously adhered to the baseplate. The optimum processing parameters for both alloys with defect-free structures at a preheat temperature of 400 • C, were at 1200-1600 W at 8-12 mm/s with the layers composed of both face centred-cubic (FCC) and body centred-cubic (BCC) phases. The laser parameters affected the quality and hardness properties of the alloys. The results showed that optimizing the laser parameters achieved by preheating temperature invariably improved the performance of the alloys with potential coatings and structural applications.
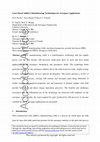
Advanced Engineering Materials, 2019
Additive manufacturing (AM) is a transformative technology that has rapidly grown over the past d... more Additive manufacturing (AM) is a transformative technology that has rapidly grown over the past decade. AM processes build parts layer by layer and have found applications in the aerospace, biomedical, and automotive fields. The technology holds particular promise for the aerospace industry due to the reduced process time, weight savings of parts, and opportunities for new material development. This article presents a review of laser-based AM processes, existing AM systems and aerospace parts being fabricated. It further explores the material properties and microstructure of printed samples with both powder bed fusion and direct energy deposition processes. The benefits and challenges associated with the widespread use of the technology are discussed with emphases on the aerospace sector. Finally, the steps required for parts produced by AM processes to become certified for use in aerospace applications are presented. 1 Introduction Three dimensional (3D) additive manufacturing (AM) is a process by which parts are built layer by layer that holds particular promise for the aerospace industry as the parts this process Accepted Article This article is protected by copyright. All rights reserved can produce may be stronger, lighter, and more efficiently designed when compared to conventional parts. Furthermore, AM technology has the ability to make one of a kind or replacement parts, faster than other processes, from anywhere (in space or underwater), and at any time. Since its inception around 30 years ago, AM has progressed from initially being used for rapid prototyping of simple geometry parts to direct part manufacturing of fully functional engine components. [1] In addition to its advantages of building freeform parts, there are other capabilities that AM technologies can offer, including localized heat treatments, surface hardening or alloying, part repair, coating application and material removal. [1] AM holds particular benefits for defense applications, such as: facilitating adaptive responses and new capabilities to counter increasingly agile adversaries, [2] creating resilient supply chains (shorten logistics tail) and enabling manufacturing at the point of need, [3, 4] increasing system availability (readiness), producing novel, high performance prototype parts, [1] repairing conventionally manufactured parts [4] and supporting reverse engineering. Although AM may not become a mainstream manufacturing technology due to its increased energy consumption, higher raw material cost and initial capital investment, its use in defense may be warranted due to the many unique attributes of this technology such as real time replacement part fabrication and in-situ repair of existing equipment. Among the many AM methods, direct metal deposition (with metal powder or wire) is best suited for defense applications for its versatility in material choice, near 100% material utilization and fast change over from one material to another. One of the final steps in a manufacturing process is shaping. For metallic or plastic/composite parts, shaping processes can be categorized into three types: (1) a removal process where machining, grinding, polishing, laser or plasma cutting and others are utilized, (2) a direct forming process involving casting, forging, sintering (powder metallurgy), stamping, injection Accepted Article This article is protected by copyright. All rights reserved molding and welding, and (3) additive manufacturing where a 3D part is made using printing (layered-by-layer or drop-by-drop), coating, welding, and brazing. [5] AM is a broad term used to describe the manufacturing of an object by adding ultrathin layers of material one by one based on a CAD model. The American Society of Testing and Materials (ASTM) has defined AM [6] as a process of joining materials to make objects from 3D model data, usually layer by layer, as opposed to subtractive manufacturing technologies. [7] Within the aerospace sector, AM of metals is of interest for structural and engine components. Laser consolidation of metals and alloys is made possible through the continuous creation of micro-welds, each building upon the previous weld to create net or near-net shape metal and alloy products. [5] For powder based AM processes, the surface finishing is determined by the powder size distribution and usually lies in the range of +/-20-50 µm, [8] requiring only minimal finish machining. All of these attributes make laser-based AM processes particularly attractive to aerospace/defense material requirements planning (MRP) operations. AM has progressed rapidly in recent years from prototyping to end-use products, [9] and it is forecasted to reach a $6.5B USD worldwide market in 2019. [10] Although AM is an emerging technology, it will not replace conventional manufacturing methods, rather the two technologies will co-exist. The introduction of AM technology will reduce part inventory, speed up production cycle time for small orders and have the ability to make a full spectrum of parts on site. Due to the rapid development of AM processes in recent years, numerous reviews have been published outlining various aspects of the technology and its applications. Reviews written by Frazier [7] and Ahmed [11] focus on the various AM processes and equipment while those by Kok et al., [12] Fayazfar et al., [13] and Lewandowski and Seifi [14] overview the microstructure and mechanical properties of printed materials. This paper introduces several AM processes Accepted Article This article is protected by copyright. All rights reserved that are of interest to the aerospace industry and provides an overview of the various equipment suppliers. Numerous companies have already begun to procure these systems and experimented with part design and production. However, parts produced by AM processes have not yet gone into mass production as the requirements to validate an AM process and the parts it produces are very strict. This paper aims to bridge the gap by first providing a state of the art on AM in the aerospace industry followed by an overview of the regulations developed by aviation authorities that are applicable to parts produced by AM. 2 Additive Manufacturing Technology Background The AM process takes the conventional engineering design loop presented in Figure 1 and introduces several phases where improvements can be made. First in the design stage, the topology (distribution of material within the finished component) has the potential to be varied from a complete solid to a porous, organic structure. [15] This is known as design for additive manufacturing (DfAM) and a further description is provided in Section 4.1. The main amendment to the design loop occurs in the fabrication stage with the introduction of the AM technologies outlined throughout this review. The optimization stage, which is used to further enhance the design, also benefits from methods used to reduce weight such as the soft kill option, [16] whereas with conventional manufacturing, these methods were seen as unfeasible or impractical. AM processes differ from conventional manufacturing (CM) processes in a variety of areas as illustrated in Figure 2. First, CM processes begin with a solid billet of material which is machined down (i.e., a subtractive process) to finished size whereas AM processes are constructive whereby material is deposited layer by layer to form a solid part which would then be followed by a final machining stage to achieve the desired dimensions, tolerances, and surface finish. As a result, AM processes generate significantly less scrap material when

Matériaux & Techniques
The past two decades have witnessed increased research in natural fibre polymer composites due to... more The past two decades have witnessed increased research in natural fibre polymer composites due to their low cost and environmental friendliness over synthetic counterparts. This has been further advanced by the global circular economy drive stressing on materials sustainability in production process. Hybridization technique has proved successful in enhancing the functional performance of natural fibre composites for advanced bulletproof and ballistic body armors applications. Laminate thickness, layering sequence, fibre loading and weaving architecture influence the ballistic performance of natural/synthetic fibre hybrid composites. Literature shows an increasing trend in research studies in natural/synthetic hybrid composites in the last twenty years to address the challenge of fibre/matrix incompatibility causing lower properties. Appropriate stacking sequence and incorporation of small quantities of nanofillers improve ballistic properties of natural fibre-based composites equiva...
Journal of Materials Science Research and Reviews, Oct 23, 2021

Graphite from Saman-Burkono in Ningi Local Government Area of Bauchi State was collected in lumps... more Graphite from Saman-Burkono in Ningi Local Government Area of Bauchi State was collected in lumps, reduced to size using geological hammer and further crushed and grinded using Denver Jaw crusher (Model KJH23) and Denver ball mill (Model 101A) respectively. Coned and Quartering sampling method was used to draw a good representative sample passing through 200µm sieve size. Chemical characterization (Proximate analysis) of the graphite’s head sample showed that it contained SiO2, Al2O3, Fe2O3, K2O, TiO2, MnO, V2O5, Cr2O3 and PbO in different proportions, with silica (SiO2) having the highest composition of 67.14%. The analysis indicated that the carbon content in the crude graphite was far below 70% which is the required standard for the suitability of graphite ore for crucible production, hence the need for beneficiation using the method of froth flotation with Kerosene as the frothier in the presence of pine oil as the collector and sodium hydroxide as the pH regulator with flotatio...
Handbook of Nanomaterials and Nanocomposites for Energy and Environmental Applications, 2020
Copyright: 2020, Switzerland: Springer. Due to copyright restrictions, the attached PDF file cont... more Copyright: 2020, Switzerland: Springer. Due to copyright restrictions, the attached PDF file contains the abstract of the full-text item. For access to the full-text item, please consult the publisher's website.
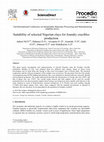
Procedia Manufacturing, 2019
This paper reports investigation and characterization of selected Nigerian clays for Foundry Cruc... more This paper reports investigation and characterization of selected Nigerian clays for Foundry Crucible production. Samples of Clay were obtained from two different sites, namely: Ipinsa in Akure Local Government area in Ondo State and Tsaragi in Edu Local Government Area of Kwara State. The chemical composition and the refractory properties of the samples were carried out. The specimens from the Clay sample were prepared using ASTM standard specification, they were subjected to selected refractory, physical, thermal and mechanical properties. The results obtained showed that the refractoriness of Tsaragi clay was 1600 o C and that of Ipinsa clay was 1370 o C. The overall results showed that both samples can be used for crucible production but it was discovered that samples from Tsaragi were found to be more suitable with reference to the value obtained in terms of Refractoriness, thermal conductivity (2.32 W/m/k) and cold crushing strength (7.5mPa) than Ipinsa sample, these values when compared with the standard specification as reported in literature, this can, therefore, be recommended for the production of foundry crucibles
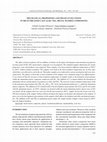
The effect of heat treatment with an addition of titania on the phase development and mechanical ... more The effect of heat treatment with an addition of titania on the phase development and mechanical properties of sand casted Al-SiC-TiO2 metal matrix composite was investigated. The standard samples dimensions for tensile properties, wear and hardness were prepared. These samples were heat treated at different temperature of 180°C to 220°C without solution treatment. The samples were held at the heat treatment temperature for an hour after which they were allowed to cool in the air. Thereafter, samples were subjected to various mechanical and wear tests, respectively. The phases evolved due to heat treatment of the samples were examined using X-ray diffractometry. It was observed that the increase in heat treatment temperature of samples leads to the formation of precipitates within the aluminium matrix composite reinforced with SiC. The addition of 5 % titania inhibits the formation of aluminium silicon carbide phases in preference to SiO2 and TiO2 . The increase in heat treatment te...
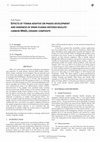
Effects of varied contents of titania on the phase development and properties of spark plasma sin... more Effects of varied contents of titania on the phase development and properties of spark plasma sintered (SPS) mullite-carbon- MnO2 ceramic composite was investigated. The raw materials used were kaolin clay, graphite, manganese oxide and titania. Samples were prepared by blending pre-calculated amounts of raw materials in Turbular mixer at a speed of 72 rev/min. The homogenous mixture were sintered in the SPS machine at 1000°C at a sintering pressure of 40 MPa, heating rate of 50°C/min and holding time of 10 min in a graphite die of 20mm. The phases in the sintered samples were characterized using x-ray diffractometry analysis (XRD). Microstructure of the samples were examined using scanning electron microscope (SEM). Harness of the sintered samples was also investigated using Vickers hardness tester. It was observed that the phases evolved in the sample were influenced by titania content. The presence of Mn2O3 in the sample lead to formation of silimanite in preference to mullite wh...
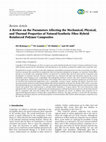
Advances in Materials Science and Engineering, 2022
The global drive towards a circular economy that emphasizes sustainability in production processe... more The global drive towards a circular economy that emphasizes sustainability in production processes has increased the use of agro-based raw materials like natural fibres in applications that have long been dependent on inorganic raw materials. Natural fibres provide an eco-friendly, more sustainable, and low cost alternative to synthetic fibres that have been used for a long time in the development of composite materials. However, natural fibres are associated with high water absorption capacity due to their hydrophilic nature leading to poor compatibility with hydrophobic polymeric matrices, thus lower mechanical properties for various applications. Hybridization of natural fibres with synthetic fibres enhances the mechanical performance of natural fibres for structural and nonstructural applications such as automobile, aerospace, marine, sporting, and defense. There have been increased research interests towards natural/synthetic fibre hybrid composites in the past two decades (200...
Leonardo Journal of Sciences, 2009
Effect of Sodium nitrite as a corrosion inhibitor of mild steel in sea water wasinvestigated, usi... more Effect of Sodium nitrite as a corrosion inhibitor of mild steel in sea water wasinvestigated, using the conventional weight loss method. Differentpercentages of sodium nitrite were used from 0% to 10% in sea water.Samples of mild steel were exposed to these corrosive media and the weightloss was calculated at intervals of 120 hours, 168 hours, 208 hours, 256 hours,304 hours and 352 hours. It was observed that corrosion rate increases withtime of exposure to the corrosive medium (inhibited or non-inhibited) and thatsodium nitrite can be used to retards the corrosion rate of mild steel if theappropriate concentration is used in sea water. It was concluded that theoptimum percentage of sodium nitrate in sea water that gives the optimumcorrosion inhibition of mild steel is 4%.
Uploads
Papers by Prof Fatai O Aramide