Soft Robotics by Tommaso Ranzani
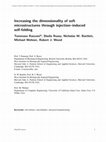
Advanced Materials, 2018
Devices fabricated using soft materials have been a major research focus of late, capturing the a... more Devices fabricated using soft materials have been a major research focus of late, capturing the attention of scientists and laypersons alike in a wide range of fields, from microfluidics to robotics. The functionality of such devices relies on their structural and material properties; thus, the fabrication method is of utmost importance. Here, multilayer soft lithography, precision laser micromachining, and folding to establish a new paradigm are combined for creating 3D soft microstructures and devices. Phase‐changing materials are exploited to transform actuators into structural elements, allowing 2D laminates to evolve into a third spatial dimension. To illustrate the capabilities of this new fabrication paradigm, the first “microfluidic origami for reconfigurable pneumatic/hydraulic” device is designed and manufactured: a 12‐layer soft robotic peacock spider with embedded microfluidic circuitry and actuatable features.

Soft pneumatic actuators are promising candidates for micro-manipulation and delicate gripping du... more Soft pneumatic actuators are promising candidates for micro-manipulation and delicate gripping due to their wide range of motion and ease of fabrication. While existing elastomer-based devices have attracted attention due to their compliant structures, there is a need for materials that combine flexibility, controllable actuation, and robustness. This paper bridges this capability gap by introducing a novel fabrication strategy for nanofiber-reinforced soft micro-actuators. The design and manufacturing of composite PDMS/nanofiber actuators using soft lithography and rotary jet spinning is described. We examine the impact of lamina design and fiber orientation on actuator curvature, mechanical properties, and pressurization range. Composite actuators displayed a 25.8% higher maximum pressure than pure PDMS devices. Further, the best nanofiber-reinforced laminates tested were 2.3 times tougher than the control PDMS material while maintaining comparable elongation. Finally, bending and bending-twisting are demonstrated using pristine and laser-patterned nanofiber sheets, respectively.
Flexible endoscopes are still the gold standard in most natural orifice translumenal endoscopic s... more Flexible endoscopes are still the gold standard in most natural orifice translumenal endoscopic surgery (NOTES) procedures; however their flexibility (necessary for navigating through the GI tract) limits their capabilities in terms of distal manipulation and stability. We propose a deployable endoscopic add-on aimed at locally counteract-ing forces applied at the tip of an endoscope. We analyze different designs: a fully soft version and two hybrid soft-folded versions. The hybrid designs exploit either an inextensible structure pressurized by a soft actuator or the stiffness provided by the unfolded " magic cube " origami structure. We focus on the fabrication and experimental characterization of the proposed structures and present some preliminary designs and integration strategies to mount them on top of current flexible endoscopes.

This paper presents the concept design of a modular soft manipulator for minimally invasive surge... more This paper presents the concept design of a modular soft manipulator for minimally invasive surgery. Unlike traditional surgical manipulators based on metallic steerable needles, tendon-driven mechanisms, or articulated motorized links, we combine flexible fluidic actuators to obtain multidirectional bending and elongation with a variable stiffness mechanism based on granular jamming. The idea is to develop a manipulator based on a series of modules, each consisting of a silicone matrix with pneumatic chambers for 3-D motion, and one central channel for the integration of granular-jamming-based stiffening mechanism. A bellows-shaped braided structure is used to contain the lateral expansion of the flexible fluidic actuator and to increase its motion range. In this paper, the design and experimental characterization of a single module composed of such a manipulator is presented. Possible applications of the manipulator in the surgical field are discussed.

This paper introduces a novel, bioinspired manipulator for minimally invasive surgery (MIS). The ... more This paper introduces a novel, bioinspired manipulator for minimally invasive surgery (MIS). The manipulator is entirely composed of soft materials, and it has been designed to provide similar motion capabilities as the octopus's arm in order to reach the surgical target while exploiting its whole length to actively interact with the biological structures. The manipulator is composed of two identical modules (each of them can be controlled independently) with multi-directional bending and stiffening capabilities, like an octopus arm. In the authors' previous works, the design of the single module has been addressed. Here a two-module manipulator is presented, with the final aim of demonstrating the enhanced capabilities that such a structure can have in comparison with rigid surgical tools currently employed in MIS. The performances in terms of workspace, stiffening capabilities, and generated forces are characterized through experimental tests. The combination of stiffening capabilities and manipulation tasks is also addressed to confirm the manipulator potential employment in a real surgical scenario.

Most devices for single-site or natural orifice transluminal surgery are very application specifi... more Most devices for single-site or natural orifice transluminal surgery are very application specific and, hence, capable of effectively carrying out specific surgical tasks only. However, most of these instruments are rigid, lack a sufficient number of degrees of freedom (DOFs), and/or are incapable of modifying their mechanical properties based on the tasks to be performed. The current philosophy in commercial instrument design is mainly focused on creating minimally invasive surgical systems using rigid tools equipped with dexterous tips. Only few research efforts are aimed at developing flexible surgical systems, with many DOFs or even continuum kinematics. The authors propose a radical change in surgical instrument design: away from rigid tools toward a new concept of soft and stiffness-controllable instruments. Inspired by biology, we envision creating such soft and stiffnesscontrollable medical devices using the octopus as a model. The octopus presents all the capabilities requested and can be viewed as a precious source of inspiration. Several soft technologies are suitable for meeting the aforementioned capabilities, and in this article a brief review of the most promising ones is presented. Then we illustrate how specific technologies can be applied in the design of a novel manipulator for flexible surgery by discussing its potential and by presenting feasibility tests of a prototype responding to this new design philosophy. Our aim is to investigate the feasibility of applying these technologies in the field of minimally invasive surgery and at the same time to stimulate the creativeness of others who could take the proposed concepts further to achieve novel solutions and generate specific application scenarios for the devised technologies.

This paper describes a multi-fingered haptic palpation method using stiffness feedback actuators ... more This paper describes a multi-fingered haptic palpation method using stiffness feedback actuators for simulating tissue palpation procedures in traditional and robot-assisted minimally invasive surgery. Soft tissue stiffness is simulated by changing the stiffness property of the actuator during palpation. For the first time, granular jamming and pneumatic air actuation are combined together to realize stiffness modulation. The stiffness feedback actuator is validated by stiffness measurements in indentation tests and through stiffness discrimination based on a user study. According to the indentation test results, the introduction of a pneumatic chamber to granular jamming can amplify the stiffness variation range and reduce hysteresis of the actuator. The advantage of multi-fingered palpation using the proposed actuators is proven by the comparison of the results of the stiffness discrimination performance using two-fingered (sensitivity: 82.2%, specificity: 88.9%, positive predicative value: 80.0%, accuracy: 85.4%, time: 4.84 s) and single-fingered (sensitivity: 76.4%, specificity: 85.7%, positive predicative value: 75.3%, accuracy: 81.8%, time: 7.48 s) stiffness feedback.

This paper introduces a pose-sensing system for soft robot arms integrating a set of macrobend st... more This paper introduces a pose-sensing system for soft robot arms integrating a set of macrobend stretch sensors. The macrobend sensory design in this study consists of optical fibres and is based on the notion that bending an optical fibre modulates the intensity of the light transmitted through the fibre. This sensing method is capable of measuring bending, elongation and compression in soft continuum robots and is also applicable to wearable sensing technologies, e.g. pose sensing in the wrist joint of a human hand. In our arrangement, applied to a cylindrical soft robot arm, the optical fibres for macrobend sensing originate from the base, extend to the tip of the arm, and then loop back to the base. The connectors that link the fibres to the necessary opto-electronics are all placed at the base of the arm, resulting in a simplified overall design. The ability of this custom macrobend stretch sensor to flexibly adapt its configuration allows preserving the inherent softness and compliance of the robot which it is installed on. The macrobend sensing system is immune to electrical noise and magnetic fields, is safe (because no electricity is needed at the sensing site), and is suitable for modular implementation in multi-link soft continuum robotic arms. The measurable light outputs of the proposed stretch sensor vary due to bend-induced light attenuation (macrobend loss), which is a function of the fibre bend radius as well as the number of repeated turns. The experimental study conducted as part of this research revealed that the chosen bend radius has a far greater impact on the measured light intensity values than the number of turns (if greater than five). Taking into account that the bend radius is the only significantly influencing design parameter, the macrobend stretch sensors were developed to create a practical solution to the pose sensing in soft continuum robot arms. Henceforward, the proposed sensing design was benchmarked against an electromagnetic tracking system (NDI Aurora) for validation.

This article introduces a soft and stretchable sensor composed of silicone rubber integrating a c... more This article introduces a soft and stretchable sensor composed of silicone rubber integrating a conductive liquid-filled channel with a biocompatible sodium chloride (NaCl) solution and novel stretchable gold sputtered electrodes to facilitate the biocompatibility of the sensor. By stretching the sensor, the cross section of the channel deforms, thus leading to a change in electrical resistance. The functionalities of the sensor have been validated experimentally: changes in electrical resistance are measured as a function of the applied strain. The experimentally measured values match theoretical predictions, showing relatively low hysteresis. A preliminary assessment on the proposed sensor prototype shows good results with a maximum tested strain of 64%. The design optimization of the saline solution, the electrodes, and the algebraic approximations derived for integrating the sensors in a flexible manipulator for surgery has been discussed. The contribution of this article is the introduction of the biocompatible and stretchable gold sputtered electrodes integrated with the NaCl-filled channel rubber as a fully biocompatible solution for measuring deformations in soft and stretchable medical instruments.

Soft Robotics, 2014
Soft robotics for medical, endoscopic applications requires a dexterous and compliant mechanism t... more Soft robotics for medical, endoscopic applications requires a dexterous and compliant mechanism to increase accessibility and decrease patient injury. However, soft structures do not offer the level of image and platform stability provided by rigid structures. Thus, a variable stiffness mechanism is an ideal solution to reconcile the two requirements of compliance and stability; the mechanism explored here is granular jamming. Granular jamming is a phenomenon where particulate matter within a membrane can transition from a fluid-like to a solid-like state, based on the level of applied vacuum pressure. In the solid-like jammed state, the conventional assumption is made that granule-granule contacts dominantly contribute to the system's stiffness. Thus, many works have evaluated the effects of different granule types by experimentally varying the sizes, shapes, and material properties of the particles. However, the role of the membrane in determining the possible range of stiffness or the variability of granular jamming has not been well studied. This paper investigates the effects and significance of membranes for a granular jamming system. Several membranes were experimentally tested and analyzed in order to find the amount of flexibility and stiffness they provide when the system is in an unjammed and jammed state, respectively. This paper presents for the first time that the membrane plays a significant contributing factor in granular jamming stiffness.
ABSTRACT This paper presents the design of a single module composing a modular soft variable stif... more ABSTRACT This paper presents the design of a single module composing a modular soft variable stiffness manipulator for minimal access surgery. The module exploits flexible fluidic actuation for obtaining multi directional bending and elongation capabilities. A novel flexible crimped braided sheath is introduced in order to increase the performances of the flexible actuator. Granular jamming based stiffening mechanism is used to tune the stiffness of the module. The fabrication of the module is described and the performances in terms of bending, elongation and stiffening are reported.

IEEE SENSORS 2014 Proceedings, 2014
This work aims at demonstrating the possibility of using advanced nanocomposite materials with tu... more This work aims at demonstrating the possibility of using advanced nanocomposite materials with tuned features in order to develop innovative pressure and deformation sensors suitable for a series of applications, including sensorization in narrow environments, implanted deformable devices, artificial skin and flexible multifunctional surgical instruments. By combining metal sputtering and spin-assisted deposition, we developed thin and flexible polymeric membranes made of polydimethylsiloxane doped with barium titanate nanoparticles, carbon nanotubes and boron nitride nanotubes. By exploiting their piezoelectric properties, the nanocomposites were able to transduce applied pressures and strains into electrical signals. Different combinations of nanoparticles, embedded in the polymeric matrix, were tested. We also highlighted the possibility to tune matrix stiffness, thus adding a "degree of freedom" in the development of nanocomposite sensing elements.
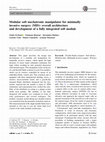
This paper describes the design and
development of a modular soft manipulator for
minimally invas... more This paper describes the design and
development of a modular soft manipulator for
minimally invasive surgery, which equals the high
dexterity of classic hyper redundant continuum, but
rigid, robots resulting in safer potential interaction
with internal organs. The manipulator relies on the use
of a soft flexible fluidic actuator in each of its modules,
which can be wireless controlled by means of an
embedded fluidic control unit. This actuation unit is
equipped with three miniaturized latching valves, a
wireless microcontroller board, and a specifically
designed fluidic distributor integrated into the elastomeric
material that the module is made of. FEM
simulations and experimental tests verified the reliability
of the distributor in acting as a piping system
inside each module. The mobility of the fully
integrated soft module was evaluated in terms of
static performances and covered workspace. The
module’s dynamic model during one-chamber motion
was estimated from the parameter estimation analysis.
The characterization of the single module behaviour is
intended as first step to ease the future high level
control of the multi-modular architecture.

This paper presents the concept design, the fabrication and the experimental characterization of ... more This paper presents the concept design, the fabrication and the experimental characterization of a unit of a modular manipulator for minimal access surgery. Traditional surgical manipulators are usually based on metallic steerable needles, tendon driven mechanisms or articulated motorized links. In this work the main idea is to combine flexible fluidic actuators enabling omnidirectional bending and elongation capability and the granular jamming phenomenon to implement a selective stiffness changing. The proposed manipulator is based on a series of identical modules, each one consisting of a silicone tube with pneumatic chambers for allowing 3D motion and one central channel for the implementation of the granular jamming phenomenon for stiffening. The silicone is covered by a novel bellows-shaped braided structure maximizing the bending still limiting lateral expansion. In this paper one single module is tested in terms of bending range, elongation capability, generated forces and stiffness changing.

This paper describes a multi-fingered haptic palpation method using stiffness feedback actuators ... more This paper describes a multi-fingered haptic palpation method using stiffness feedback actuators for simulating tissue palpation procedures in traditional and robot-assisted minimally invasive surgery. Soft tissue stiffness is simulated by changing the stiffness property of the actuator during palpation. For the first time, granular jamming and pneumatic air actuation are combined together to realize stiffness modulation. The stiffness feedback actuator is validated by stiffness measurements in indentation tests and through stiffness discrimination based on a user study. According to the indentation test results, the introduction of a pneumatic chamber to granular jamming can amplify the stiffness variation range and reduce hysteresis of the actuator. The advantage of multi-fingered palpation using the proposed actuators is proven by the comparison of the results of the stiffness discrimination performance using two-fingered (sensitivity: 82.2%, specificity: 88.9%, positive predicative value: 80.0%, accuracy: 85.4%, time: 4.84 s) and single-fingered (sensitivity: 76.4%, specificity: 85.7%, positive predicative value: 75.3%, accuracy: 81.8%, time: 7.48 s) stiffness feedback.
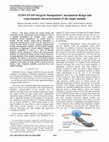
This paper presents the concept design, the fabrication and the experimental characterization of ... more This paper presents the concept design, the fabrication and the experimental characterization of a unit of a modular manipulator for minimal access surgery. Traditional surgical manipulators are usually based on metallic steerable needles, tendon driven mechanisms or articulated motorized links. In this work the main idea is to combine flexible fluidic actuators enabling omnidirectional bending and elongation capability and the granular jamming phenomenon to implement a selective stiffness changing. The proposed manipulator is based on a series of identical modules, each one consisting of a silicone tube with pneumatic chambers for allowing 3D motion and one central channel for the implementation of the granular jamming phenomenon for stiffening. The silicone is covered by a novel bellows-shaped braided structure maximizing the bending still limiting lateral expansion. In this paper one single module is tested in terms of bending range, elongation capability, generated forces and stiffness changing.
3rd Joint Workshop on New Technologies for Computer/Robot Assisted Surgery 11-12-13 September 2013, Verona, Italy, Sep 13, 2013
This paper presents the design of a single module composing a modular soft variable stiffness man... more This paper presents the design of a single module composing a modular soft variable stiffness manipulator for minimal access surgery. The module exploits flexible fluidic actuation for obtaining multi directional bending and elongation capabilities. A novel flexible crimped braided sheath is introduced in order to increase the performances of the flexible actuator. Granular jamming based stiffening mechanism is used to tune the stiffness of the module. The fabrication of the module is described and the performances in terms of bending, elongation and stiffening are reported.
Uploads
Soft Robotics by Tommaso Ranzani
development of a modular soft manipulator for
minimally invasive surgery, which equals the high
dexterity of classic hyper redundant continuum, but
rigid, robots resulting in safer potential interaction
with internal organs. The manipulator relies on the use
of a soft flexible fluidic actuator in each of its modules,
which can be wireless controlled by means of an
embedded fluidic control unit. This actuation unit is
equipped with three miniaturized latching valves, a
wireless microcontroller board, and a specifically
designed fluidic distributor integrated into the elastomeric
material that the module is made of. FEM
simulations and experimental tests verified the reliability
of the distributor in acting as a piping system
inside each module. The mobility of the fully
integrated soft module was evaluated in terms of
static performances and covered workspace. The
module’s dynamic model during one-chamber motion
was estimated from the parameter estimation analysis.
The characterization of the single module behaviour is
intended as first step to ease the future high level
control of the multi-modular architecture.
development of a modular soft manipulator for
minimally invasive surgery, which equals the high
dexterity of classic hyper redundant continuum, but
rigid, robots resulting in safer potential interaction
with internal organs. The manipulator relies on the use
of a soft flexible fluidic actuator in each of its modules,
which can be wireless controlled by means of an
embedded fluidic control unit. This actuation unit is
equipped with three miniaturized latching valves, a
wireless microcontroller board, and a specifically
designed fluidic distributor integrated into the elastomeric
material that the module is made of. FEM
simulations and experimental tests verified the reliability
of the distributor in acting as a piping system
inside each module. The mobility of the fully
integrated soft module was evaluated in terms of
static performances and covered workspace. The
module’s dynamic model during one-chamber motion
was estimated from the parameter estimation analysis.
The characterization of the single module behaviour is
intended as first step to ease the future high level
control of the multi-modular architecture.
(Natural Orifice Translumenal Endoscopic Surgery) robotic
approaches to enable scarless surgical procedures. Despite of
the variegated devices proposed, they still have several
limitations. In this work, we propose a surgical platform
composed of specialized modules, in order to provide the
overall system with adequate stability, dexterity and force
generation. The concept behind the platform, the main modules
and their performance are described to highlight the system
potential to outperform current NOTES procedures.
force sensor which can be integrated with the robot arm of the
EU project STIFF-FLOP (STIFFness controllable Flexible and
Learnable Manipulator for Surgical Operations) in order to
measure applied external forces. The structure of the
STIFF-FLOP arm is free of metal components and electric
circuits and, hence, is inherently safe near patients during
surgical operations. In addition, this feature makes the
performance of this sensing system immune against strong
magnetic fields inside magnetic resonance (MR) imaging
scanners. The hollow structure of the sensor allows the
implementation of distributed actuation and sensing along the
body of the manipulator. In this paper, we describe the design
and calibration procedure of the proposed three axis
optics-based force sensor. The experimental results confirm the
effectiveness of our optical sensing approach and its
applicability to determine the force and momentum components
during the physical interaction of the robot arm with its
environment.